rto蓄熱式廢氣焚燒爐
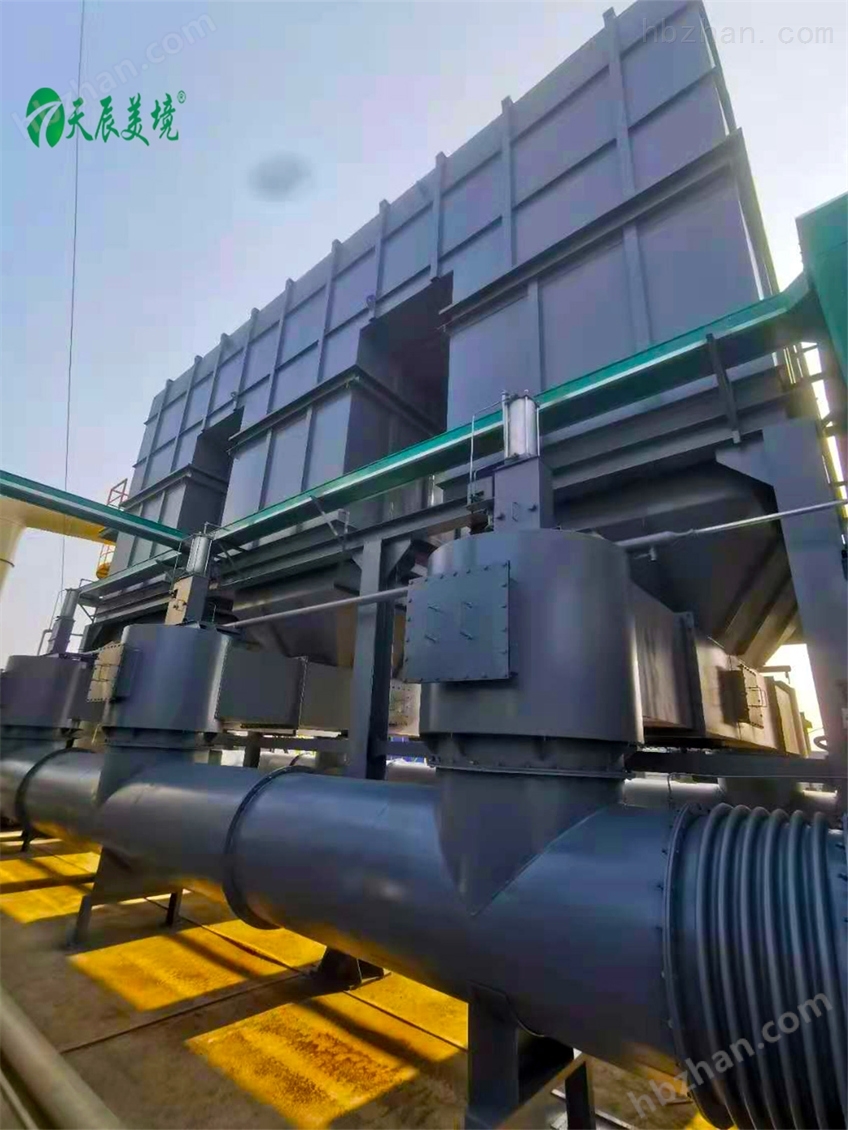
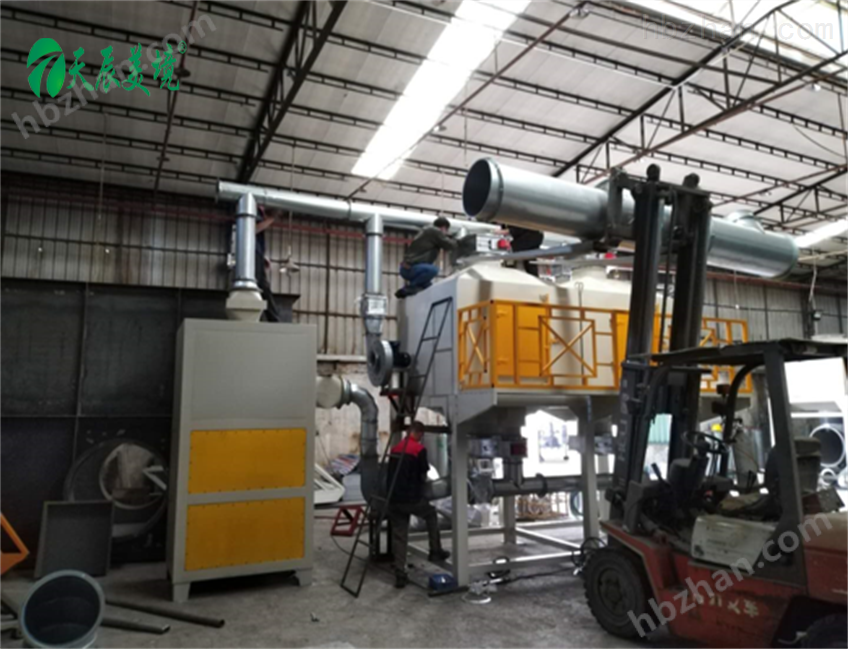
近年來,我國的醫藥化工行業得到了長足發展,特別是原料藥和醫藥中間體增長迅猛,我國已成為大的原料藥和醫藥中間體生產國,醫化行業成了一些地區的支柱產業之一,而由此產生的廢氣污染問題也成為了全社會關注的焦點。經過持續多年的環境深化整治,雖然醫化行業的廢氣污染在一定程度上得到了控制,但仍存在很多問題。
醫化行業的廢氣具有成分復雜、總體產生量大、產生量波動大、揮發性有機化合物(VOC)濃度波動大等特點。其主要污染物(如苯類、酮類、醚類、鹵代烴類等)多為有毒、有害且具惡臭性質的氣體,進入自然環境后對人體健康和生態環境危害較大,如何處理醫化行業的廢氣一直是環保領域的重點和難題。
因醫化廢氣超標排放影響周邊生活環境所引起的投訴與糾紛越來越多,在某些地區,部分中小企業因無法承擔巨額的環境治理費用,或迫于地方環保壓力不得不選擇關閉停產。醫化行業的環保門檻越來越高,環保設施投入越來越大。在這種情況下,很多醫化企業花費大量資金購置環保設備,但是因為缺乏合理的技術引導,導致大部分設備沒有發揮作用或難以發揮作用,很多環保設施成為擺設,成為應付政府環保部門檢查的形象工程。而有些環保工程公司為了追求利潤,夸大其環保設施作用,避而不談其缺點及使用條件的限制,導致社會資源浪費。某些企業環保管理人員因缺乏必要的環保專業知識,過于相信環保公司對其環保設施的介紹,認為可以一勞永逸,從另一方面增加了環保設施正常運行的難度。
1蓄熱式熱氧化爐(RTO焚燒爐)的介紹
縱觀醫化廢氣處理過程,從最初的冷凝、酸堿吸收、化學氧化到微生物滴濾、碳纖維吸附、低溫等離子、催化氧化、蓄熱式熱氧化等,可以說沒有一項技術可以通用于所有行業。以上某些技術在一些領域(如石化、汽車制造、城市污水處理等)得到了較好應用,但是不能認為就適合在醫化行業推廣,上述技術均有一定的選擇性和限制性。例如,比較*的催化氧化技術,因催化劑的選擇性較強而阻礙了其在醫化行業的應用;低溫等離子對小分子污染物作用有限,氧化不*;微生物滴濾在城市污水處理過程中用于除臭效果明顯,在醫化廢氣處理方面也有部分成功實例,其結構簡單、維護管理方便、運行費用低廉,但技術上還需要進一步研究和完善。
相對而言,蓄熱式熱氧化爐(RTO焚燒爐)因其對廢氣成分選擇性小,高溫對有機氣體破壞較*,從而具有一定優勢,但它也還存在一定的局限性。由于RTO焚燒爐在國外的研究發展歷史只有30多年,在我國只有10多年,技術上還不成熟,實際應用經驗也不夠,比如對廢氣量和VOC含量不穩定的廢氣處理運行管理難度較大,控制當會導致產生一定的安全風險等?,F階段蓄熱式熱氧化爐(RTO)并不是、最的醫化廢氣處理方法,不能從根本上解決醫化行業的廢氣污染問題。
常用RTO焚燒爐的蓄熱床為3個(也有2床及3床以上,因處理效率及實用性等原因不常用)。蓄熱床由多孔蓄熱陶瓷制成,廢氣從蓄熱床底部進入,經蓄熱床預熱,至燃燒室充分氧化放熱,再從另一床頂部進入,熱量留在蓄熱床內,然后從底部排出,1床進氣、1床蓄熱、1床吹掃(減少因進氣殘留在陶瓷中的廢氣進入尾氣,提高VOC去除率),通過進出口閥的自動切換實現上述3個過程在每一床中輪流進行。
2RTO的選材問題
醫化廢氣成分復雜,且廢氣組分中含鹵素、氮、磷、硫的有機物質,這些物質一旦經高溫焚燒后就會產生酸,對RTO焚燒爐設備造成嚴重腐蝕,甚至導致設備無法運行,而且容易導致廢氣排放口酸性物質嚴重超標。
醫化廢氣中含有的鹵素、氮、磷、硫等有機物多數來源于含這些元素的溶劑、物料及副產物。導致這些物料的揮發主要源于投料、轉料、反應、溶劑回收、抽濾、壓濾等生產階段,生產時除應盡量避免采用容易導致溶劑大量揮發的操作(如盡量少用離心機等)外,還應加強廢氣冷凝回收,采用多級冷凝、普冷與深冷結合的方式。對于像二氯甲烷這一類沸點低且含鹵素的溶劑,在冷凝回收的基礎上,建議采用碳纖維吸附裝置,提高回收效率。
在醫化行業中,杜絕含鹵素、氮、磷、硫的有機物質進入RTO焚燒爐系統是不現實也是不可能的,但必須從源頭抓起,減少使用產生這類物質的溶劑,加強車間管理,強化過程回收,優化末端治理。
對于末端治理設施RTO來說,因其運行溫度高,除蓄熱陶瓷之外的大部分材料只能選用鋼材,而酸對鋼材的腐蝕又很嚴重。這樣的條件下,雙相鋼是一個較好的選擇。在設備的制造過程中,如果設計合理,選材得當,再加上運行管理較好,RTO蓄熱床的出口溫度一般不會超過100℃,這樣,RTO在蓄熱床支架以下的部分就可以考慮采用其他工程材料或鋼材做防腐處理,如環氧樹脂、襯四氟、搪玻璃或玻璃鋼等材料,選材還必須綜合考慮強度、承重、安全要求以及異常情況等。
廢氣排放口要達標排放,RTO焚燒爐出口必須是可以吸收酸的,吸收塔的選型應綜合考慮廢氣量、酸濃度、吸收方式、吸收液種類等因素。常用吸收液為堿液,建議采用多級吸收:一級水吸收常開,二級堿液常開,三級堿液備用。堿性吸收液的堿濃度不宜過高,以免大量吸收二氧化碳生成碳酸鹽,導致塔內結垢。具體控制指標應根據實際情況控制pH值,吸收液在因鹽析出而較渾濁時進行更換,不能根據時間而定。
3RTO的運行能耗問題
如果RTO運行管理不善,車間廢氣處理控制不好,往往造成RTO運行能耗大、成本高,企業往往因過高的成本而停止運行RTO,僅僅把RTO當作形象工程。
RTO焚燒爐的運行能耗主要是電和燃料。一旦設備定型了,電耗基本恒定,風機可采用變頻控制省電,這里不做討論,主要討論燃料問題。因廢氣量不穩定、濃度不穩定,加上車間廢氣控制不好,所以在RTO啟動及運行過程中,需要經常補充燃料(常用柴油、天然氣)以維持燃燒室溫度。
燃料消耗多少,關鍵取決于蓄熱陶瓷的蓄熱能力,通常以RTO在能夠維持正常運行而不需補充燃料所需的VOC濃度來衡量RTO的能耗高低。此數值越低,則能耗越低。性能超好的RTO此數值可達450×10-6mg/L。另外,RTO的能量損耗主要是尾氣帶走的熱量和表面散熱損失,尾氣帶走熱量與廢氣量和進出口溫差相關,尾氣溫度越低、進出口溫差越大,則能耗越低。表面散熱損失體現在箱體表面溫度與環境的溫度差,保溫效果好則溫差小,散熱損失小。當然,能耗還有可能跟局部地方保溫薄弱及高溫氣體泄漏有關。
在企業選擇RTO焚燒爐時,提供給RTO設計廠家的風量及有機物濃度參考值需要綜合考慮,風量選擇過大,VOCs濃度偏小,運行能耗高。風量選擇過小,VOCs濃度偏大,容易在爐膛發生回火、閃爆等安全事故,且高濃度有機廢氣在輸送過程中也容易因靜電等發生爆炸事故。因此,設計時應適當放大風量,降低安全風險。還可以采用變頻控制等手段,根據生產情況調節風機風量,以降低能耗。
在RTO的運行過程中,應優化控制手段,在廢氣進爐膛前,盡可能除掉入口噴淋塔帶來的水分,減少水分汽化所需熱量;同時,還應優化進出風時間、保持燃燒室溫度、加強閥門密封度等,還可在進氣風管采用計量泵與蒸發器組合的方式,人為控制一些不可套用的廢溶劑的蒸發,在廢氣VOC較低時提高VOC濃度,以達到不使用燃料就能維持正常燃燒的目的,從而減少燃料消耗。一般來說,RTO維持正常運行對VOC濃度的要求遠低于其爆炸下限,還可根據爐膛溫度隨時調整或關閉廢溶劑的蒸發,所以其安全風險是可控的。
4RTO的控制手段及安全措施
關于RTO焚燒爐配套的控制手段,每個廠家各有所長。通常存在的問題是廢氣濃度異??刂啤?/p>
一般來說,廢氣濃度異常指廢氣中VOC濃度偏離RTO正常運行需要,尤其是廢氣濃度偏高容易帶來安全風險。一些廠家采取廢氣總管恒壓(廢氣總管負壓情況與引風機變頻器連鎖)以恒定廢氣流速,但是并未能夠解決VOC濃度波動問題。有一些廠家采用在VOC濃度較高時加新風稀釋的方法,此方法的關鍵問題是如何及時、準確地測定廢氣濃度,從而確定稀釋風與廢氣的比例。而如何及時、準確地測定廢氣濃度并反饋到控制系統中,這就對VOC在線監測儀的要求非常高。在企業內部,RTO與廢氣產生點的距離也就幾十米,最多幾百米,扣除數據傳輸、系統反應及相應的閥門動作所需要的時間,留給在線監測儀采樣和數據分析的時間往往只有幾秒最多幾十秒,而在線監測儀要在幾秒到幾十秒的時間內完成采樣和數據分析,困難較大,目前還沒有比較成功的案例。另外,VOC在線監測儀一般安裝在室外,使用環境較差,對VOC在線監測儀的要求更高。
對于上述問題,目前只能退而求其次,采用產點控制、后端加大新風量的方法加以應對,實際上也屬無奈之舉,因國內已經發生多起RTO回火及閃爆事故,不得不謹慎考慮。平時多對廢氣總管濃度進行取樣檢測,分析VOC濃度變化規律,對容易產生大量廢氣的點加以控制(如溶劑回收塔),運行中注意RTO蓄熱床溫度變化情況,及時調整主風機和新風風機運行頻率,可以在一定程度上降低此風險。但是要*解決此問題,還需要研究人員繼續努力。
RTO出現故障停機時,一些廠家的設計程序是主風機、新風風機都停止運行,進出口閥門自動關閉。如果閥門密封很好,這時候不會產生安全問題。但如果進出口閥密封不好,就會有廢氣和新風進入管道、爐膛,容易發生閃爆。所以,一般建議修改程序,在出現故障停機時,新風風機不能停止運行。
另外,如果突然停電,新風風機不能運行,并且進出口閥門不能自動關閉,廢氣和新風極易進入管道、爐膛,安全隱患更大。為了應對突然停電引起安全事故的情況,應考慮裝備UPS給自控系統供電。還可以考慮安裝氮氣系統,在突然停電時自動向管道、爐膛內輸送氮氣,降低系統內部的氧氣含量,以保證安全。
5RTO的進出口閥問題
由于必須在一定的時間間隔內實現蓄熱、燃燒與吹掃的頻繁切換,進出口閥成了RTO的關鍵部件之一。盡管正常情況下廢氣出口溫度不高,對進出口閥材料無特殊要求,但必須考慮進出口閥的密封性、靈活性、可靠性和使用壽命。因為廢氣中含有的微小粉塵以及頻繁動作,勢必對密封面造成磨損,這些因素應當在選用進出口閥時予以充分考慮。如果出現閥門密封不嚴、壓力損失過大、動作速度慢等問題,就會影響RTO的使用性能和節能效果。嚴重時還會出現安全問題,前面已有論述,此處不再贅述。
廢氣焚燒爐廠家
揮發性有機化合物(Volatile Organic Compounds,簡稱VOCs) 一般指沸點低于250℃的化學物質,是常見的大氣污染物,包含鹵代烴、脂肪烴、芳香烴、有機酸、硫烴等。這些有機廢氣對動植物生產、人體健康以及環境質量等均可造成造成極大的直接危害。VOCs 在陽光照射下,與大氣中的氮氧化合物、碳氫化合物發生光化學反應,引起光化學煙霧、酸雨、霾和氣候變化等一系列環境問題,這些揮發性有機廢氣在空氣中懸浮匯聚亦是導致PM2.5 和PM10 數值不斷上升的原因之一,因而如何削減這些揮發性污染物至關重要。
中國是印刷大國,據統計,具有較大規模的企業八萬多家,其中大部分油墨和涂布工業均采用油性涂料作為涂布液,因此導致每年產生的有機廢氣排放量高達幾十萬噸。這些VOCs 的排放不僅對人的身體健康造成巨大的傷害,還是原料資源的極大浪費,導致企業生產成本上升和經濟效益下降。本文根據江蘇某材料包裝生產企業含VOCs 廢氣的產排特征,采用了“三室RTO+ 熱能回收”處理工藝應用于企業廢氣的末端處理,取得了良好的經濟效益、環境效益和社會效益。
1、產污環節
企業主要產品包括PET 普通煙包轉移膜、OPP鐳射防偽轉移膜、PET 鐳射防偽轉移膜等。項目涂布、烘干工段均在涂布機上進行操作,該機由放卷、前放卷張力、糾偏系統、涂布頭、干燥箱(烘箱)、冷卻系統、后收卷糾偏、張力系統、收卷系統組成。
涂布頭包括涂布網紋輥、背輥(壓輥)、刮刀、刮刀調節機構。涂布頭是涂布機的核心部分,涂布機的技術能力取決于涂布頭。加熱采用5段式電加熱,GSN熱風循環,溫度140℃。安放在放卷裝置上的基膜(厚度12-18um) 經自動糾偏后進入浮輥張力系統,調整前放卷張力后進入涂布頭,調配好的涂料按涂布系統的設定進行連續涂布,涂布后濕膜進入干燥箱(烘箱) 由熱風進行干燥,干燥后帶信息涂層的塑料薄膜經冷卻系統冷輥定型后調整系統控制好張力、同時控制好收卷速度(80-100m/min)、使它與涂布速度同步,冷卻后的膜由糾偏系統自動糾偏使其保持在中心位置由收卷裝置進行收卷。
生產過程中會有調配廢氣、涂布廢氣,烘干廢氣產生,主要含有乙酸乙酯、醋酸正丁酯、丁酮、丙二醇甲醚等有機污染物。方案采用了蓄熱式熱氧化爐來治理生產過程中的有機廢氣,并結合余熱回收利用設備,為企業開辟一條既環保又節能的處理工藝路線。
2、設計要點
2.1 風量設計
車間調配區采用排風罩收集進行局部通風,排風罩設置在污染物上方,根據公式計算:Q= kphvx ;式中:P-排風罩口敞開面的周長,m;H-罩口至污染源距離,m;vx-污染物邊緣控制風速;k-安全系數,一般取1.4。最終確定排放量Q1為1200m3/h。
項目對涂布機頭區域進行密閉,并采用全面通風,全面通風量可根據換氣次數確定,即Q=nV,式中:n-換氣次數,1/h ;V-通風房間體積,m3。由于廠房內空間潔凈度等級為7級,根據GB50073-2001規定,換氣次數為15~25次,方案選定n=20,排放量Q2為2400m3/h。
設備烘箱配有熱風循環系統及排放裝置,其排風機額定風量Q=5000m3/h,故兩套生產線合計風量Q3=10000m3/h。
綜上所述,Q總=Q1+Q2+Q3=13600m3/h??紤]處理系統留有10%的操作余量,確定進入RTO裝置的廢氣處理能力Q=15000 m3/h。
2.2 余熱回收系統
根據項目的實際運行情況,收集廢氣的主要污染物為乙酸乙酯溶劑,其濃度為4000mg/m3,計算可知該股廢氣的熱值為365640 kcal/h,維持RTO 設備的自運行所需的能量為176023kcal/h,因此可通過換熱器等形式回收VOC 氧化后的余熱用于涂布干燥用熱,從而實現設備煙氣排放余熱回收利用的目的,熱量平衡方程式如下:
其余熱回收經濟效益計算公式如下:
189617(富余熱量)×0.7(系統綜合利用率)×24(h/d)×300(d/a)/8500( 天然氣熱值)= 112432(m3/a) ;
112432(m3/a)×3.65(元/m3)=41(萬元/a)
上面計算中,效益將隨生產線的實際工作時間(年時基數)變化而變化。
2.3 主體設備參數
該企業廢氣中不含鹵素、氮、硫等元素,腐蝕性不強,因此焚燒爐殼體采用6mm厚的Q235B鋼板密封滿焊;蓄熱陶瓷體選用采用LANTEC MLM180產品及抗硅填料混合而成,該填料在急熱急冷時具有很好的化學和物理穩定性,還可以改善氣流分布。RTO燃燒室的設計溫度需要燃燒器來維持,項目采用進口品牌霍尼韋爾低壓頭比例調節式天然氣燃燒器,雙電磁閥避免燃料不燃燒而進入爐膛,同時其具有自動吹掃、自動點火、紫外線掃描儀火焰檢測、火焰燃燒狀況監視等功能。設計主要參數如表2所示。
2.4 控制系統
完善的自動控制,是安全生產的保障。項目采用DCS系統對RTO本體及熱能回收系統進行自動控制。由于涉及多個功能區,一方面,各區域設備由于生產用能相互關聯;另一方面,設備又具有相對獨立的要求,導致各區域電控連鎖關系較為復雜,其控制要點如下:
(1) 停機狀態。RTO原始狀態,超溫安全自動閥位置:密閉,煙氣不經余熱換熱器;新風系統原始狀態,新風管路氣動閥:打開,新風風機啟動,新風始終經過余熱換熱器。
(2) 運行狀態。RTO 爐內溫度<850℃,超溫安全自動閥密閉;RTO 爐內溫度≥850℃,向DCS 系統提供高溫信號,超溫安全自動閥(耐溫960℃)打開,高溫煙氣經過余熱換熱器。
(3) 熱風溫度過高(>120℃)報警信號。出余熱換熱器后,熱風回風管上設一個溫度探頭。當熱風溫度高于120℃時,給RTO提供高溫報警信號,RTO超溫安全自動閥進行調節,減小經過余熱換熱器的高溫煙氣量。
3、運行效果
項目于2017年通過由環保三同時驗收,廢氣凈化系統出口的檢測結果見表3,結果表明經處理后的各類廢氣污染因子均能達標排放。
4、經濟分析
(1)RTO系統(包括爐體、余熱回收設備、新風風機等)總投資共計160萬元。
(2)RTO 系統有新風風機一臺11kW/h,主引風機一臺37kW/h,助燃風機一臺3kW/h,吹掃風機一臺5.5kW/h,控制柜耗電量為1.5kW/h ;按每年工作7200h計算,每度電0.75元計算,共計:(58+11)kW/h×7200h×0.75元=37萬元/年。
(3) 系統正常運行后,余熱回收經濟效益約為41萬元/年。